Polifenilen Sülfid (PPS) Enjeksiyon Kalıplama Proses Koşulları ve Ekipmanlar
Elektrikli dozaj pompaları, hassas sıvı transferi ve kimyasal dozajlama için idealdir. SCM-EB Volumetrik modelinin avantajlarını keşfedin!
1. Proses Parametreleri
Erime Sıcaklığı Aralığı:
* PPS’in erime noktası yaklaşık 280°C olmakla birlikte, enjeksiyon sırasında eriyik malzeme sıcaklığı genellikle daha yüksektir. Tipik eriyik (kovan) sıcaklık aralığı 300–340°C olarak önerilir.
* Cam elyaf veya mineral dolgu içeren PPS bileşiklerinde dolgunun iyi dağılması ve akışın iyileşmesi için 320–340°C civarında işlem sıcaklıkları yaygın olarak kullanılır.
* 350°C üzerindeki sıcaklıklardan kaçınılır; zira çok yüksek sıcaklıklar polimerde bozunmaya ve kalıpta korozyona yol açabilir.
Kalıp Sıcaklığı:
* Kalıp sıcaklığı, PPS’in kristallenmesi ve parça performansı için kritik bir parametredir. En az 135°C civarında veya tercihen daha yüksek kalıp sıcaklıkları önerilir.
* 135°C üzerindeki kalıp sıcaklıklarında PPS hızlı bir şekilde kristalize olarak parçada yüksek boyutsal kararlılık sağlar. Özellikle yüksek sıcaklık ortamında kullanılacak parçalar 135°C veya üzerinde bir kalıp sıcaklığında kalıplanmalıdır.
* Kalıp sıcaklığını 120°C’nin altına düşürmekten kaçınmak tavsiye edilir; düşük kalıp sıcaklıkları parçada düşük kristallenme ile sonuçlanıp, daha sonraki kullanımda boyutsal değişkenliğe neden olabilir.
* Uygulamada 130–150°C aralığı tipiktir ve yaklaşık 150°C kalıp sıcaklığı yaygın olarak kullanılmaktadır.
Enjeksiyon Basıncı:
* PPS malzemesi, camsı eriyik viskozitesine rağmen dolgu malzemeleri sayesinde iyi akış gösterir ve ince kesitli parçaları doldurabilir. Enjeksiyonun birinci kademe doldurma basıncı genellikle 30–100 MPa aralığında ayarlanır.
* İnce cidarlı veya karmaşık parçaları tam olarak doldurmak için aralığın üst sınırına (yüksek basınca) ihtiyaç duyulabilir. Ancak, çok yüksek enjeksiyon basıncı kalıp ayrımlarından flaş (çapak) oluşumuna sebep olabileceği için, parçanın görünümü ve dolumu tatmin edici olduğu sürece mümkün olan en düşük basınç kullanılmalıdır.
* Yüksek hızlı dolum gereken durumlarda basınç artacaktır; iyi yüzey kalitesi elde edildikten sonra daha fazla basınç yükseltmek anlamsız kabul edilir.
Tutma (Ütüleme) Basıncı:
* İkinci kademe tutma basıncının amacı, kalıp dolduktan sonra eriyik büzülürken iç boşluk bırakmamak ve parçayı yoğunlaştırmaktır. Tutma basıncı değeri, malzemenin cinsine ve parça geometrisine göre değişse de enjeksiyon basıncına yakın veya biraz altında bir değer genellikle kullanılır. Özellikle yüksek dolgu (ör. cam elyaf) içeren PPS bileşiklerinde ~700 bar (70 MPa) gibi yüksek tutma basınçlarının parçayı tam ütüleme için başarıyla uygulandığı bildirilmiştir.
* Tutma basıncı süresi de yeterli yoğunluğu sağlamak üzere optimize edilmelidir (örneğin 5–10 saniye arası, parça kalınlığına bağlı olarak).
Soğutma Süresi ve Kalıp Açma Zamanı:
* PPS yarı kristalin bir polimer olduğu için, kalıp içinde yeterli soğutma süresi parçada istenen kristal yapının oluşması ve biçim kararlılığı için önemlidir. Kalıbın yüksek sıcaklıkta olması (ör. ~150°C), parçanın kalıpta yavaş soğuması anlamına gelir; bu nedenle parça yeterince sertleşene kadar kalıbın kapalı kalma süresi genellikle diğer mühendislik plastiklerine kıyasla biraz daha uzun olabilir. Eğer parça kalıptan çıktığında hâlâ çok sıcaksa soğutma süresi artırılmalı veya kalıp sıcaklığı 135–149°C aralığında tutulmalıdır.
* Tipik kalıp soğutma (kalıp kapalı) süreleri, parça et kalınlığı ve geometrisine bağlı olarak değişir; ince duvarlı parçalar için birkaç saniye yeterliyken, kalın kesitli parçalarda on saniyeler mertebesine çıkabilir. Kalıp açma zamanı, parçanın yeterli sertliğe ulaştığı ana denk getirilmelidir. Parça hala yarı yumuşak halde çıkıyorsa, kalıptan sonra bir soğutma fikstürüne konulması önerilir. Nitekim, PPS parçalarında bükülme/çarpılma riskine karşı kalıp sonrası soğutma fikstürü kullanılması iyi bir uygulamadır
* Bu şekilde parça kalıptan alındıktan sonra kontrollü biçimde soğutularak boyutsal stabilite artırılır.
2. Kullanılan Yardımcı Ekipmanlar
Kurutucular:
* PPS bileşiklerindeki mineral dolgular nem tutabilmektedir.
* Nemli hammadde, enjeksiyon sırasında eriyik içinde buhar oluşmasına ve yüzeyde “splay” adı verilen gümüşü beyaz izlere veya malzeme bozunmasına yol açabilir. Bu nedenle kalıplama öncesinde granül hammaddeyi kurutmak şarttır. 135–150°C sıcaklıklarda 2–4 saatlik bir kurutma, genellikle PPS bileşiklerini güvenle işlemeye yeterli hale getirir.
* Örneğin, 140°C’de 3 saatlik bir ön kurutma tavsiye edilmektedir.
* Basit fırınlarda nemli hava sirkülasyonu sınırlı olabildiğinden, tercihen nem alıcı özellikli (desikant) kurutucular kullanılmalıdır. -40°C çiğ noktası seviyesinde kuru hava üfleyen endüstriyel kurutucular, 149°C giriş havasıyla 2 saat gibi bir sürede PPS’i etkin şekilde kurutabilir.
* Uzun süre depoda beklemiş veya paketini açtıktan sonra ortama maruz kalmış PPS malzemesi, işleme girmeden önce mutlaka bu şekilde kurutulmalıdır.
Enjeksiyon Makinesi Özellikleri:
* PPS, malzemenin yüksek işleme sıcaklığına uygun bir makine olmasına dikkat edilmelidir (vida silindiri 340°C civarına kadar ısıtılabilmeli). Makine seçiminde, Enjeksiyon kapasitesinin üretilen parçanın baskı hacmiyle dengeli olmasına özen gösterilir. Silindirin çok büyük olması, PPS eriyiğinin silindir içinde gereğinden uzun süre kalmasına ve termal olarak bozulmasına (renk koyulaşması, çapaklanma) neden olabilir.
* Enjeksiyon vidasının tasarımı da orta-yüksek basınçlı mühendislik plastiklerine uygun olmalıdır; L/D oranı genelde 16–20:1 ve sıkıştırma oranı ~2.5:1 değerlerinde, genel amaçlı vida profili PPS için yeterlidir.
* Geri akış önleyici (check ring) valfin sağlam ve etkin çalışması özellikle önemlidir; çünkü PPS’in düzgün ütülenmesi ve her çevrimde tutarlı bir yastık (cushion) bırakılması buna bağlıdır.
* Bilye tip çek valf yerine uzun vadede daha güvenilir olan halka tip çek valf tercih edilmelidir.
* Enjeksiyon makinesi memesi genelde açık tip kullanılabilir, ancak yüksek sıcaklıkta PPS eriyiğinin kalıp bekleme anında sızmasını önlemek için shut-off (kendini kapatan) memelerde kullanılmaktadır. Makine kontrolünde enjeksiyon sonrası vidanın bir miktar geriye çekilerek memedeki eriyik basıncını azaltması (dekompresyon) da PPS için yaygın bir uygulamadır; bu sayede düşük viskoziteli PPS eriyiğinin meme ucundan akması engellenir.
* Yüksek dolgu oranlı PPS, makine kovan ve vidasında ciddi aşınmaya yol açabileceğinden, bimetalik kovan vida kullanılmalı ve ayrıca düzenli olarak aşınma-korozyon kontrolü yapılmalıdır.
Kalıp Tasarımı (Havalandırma ve Soğutma):
* PPS malzemesi, diğer termoplastikler gibi uygun tasarlanmış bir kalıp gerektirir ancak yüksek sıcaklık dayanımı ve dolgu aşındırıcılığı gibi etkenler özel dikkate alınmalıdır. Havalandırma (vent) kanalları, kalıp tasarımında özellikle önemlidir. Yüksek enjeksiyon hızlarında, kalıp içindeki hava yeterince kaçamazsa sıkışıp yanarak parçada yanık izleri oluşturabilir. Bu nedenle kalıbın özellikle akışın sonlandığı uç bölgelerinde ve kilitli cep noktalarında havalandırma boşlukları bulunmalıdır. Tipik olarak PPS için havalandırma yarıkları 0.008–0.013 mm (8–13 mikron) derinlikte tutulur ve yaklaşık 1.5–2 mm uzun bir kanal arazi (land) kısmı bırakılır.
* İnce ve derin olmayan bu havalandırma oyukları, eriyik malzemenin taşmasına izin vermeden havayı dışarı atacak şekilde tasarlanır. Eğer kalıp havalandırması yetersizse, enjeksiyon hızını yavaşlatmak yanık izlerini bir miktar azaltabilir; ancak bu çözüm yerine doğru venting tasarımı tercih edilmelidir.
* Kalıp malzemesi seçiminde de, PPS’in dolgu maddelerinin aşındırıcılığı göz önüne alınmalıdır. Kalıp çekirdekleri ve kaviteleri için mümkünse sertleştirilmiş takım çelikleri (ör. HRC 58-60 sertliklerinde A2, D2 gibi çelikler) kullanılmalı veya en azından yüzeyleri sert krom, nikel alaşımı gibi kaplamalarla güçlendirilmelidir.
* Özellikle cam elyaf takviyeli PPS, Mohs 5–7 sertlikte aşındırıcı bir karaktere sahip olduğundan, kalıp yolluk girişleri, kapak yüzeyleri gibi yüksek aşınmaya maruz bölgelerde sökülebilir-bileşenler (ör. sert metal enjeksiyon burçları, değiştirilebilir giriş yuvaları) kullanılması bakım kolaylığı sağlar.
Soğutma (Isıtma) sistemleri:
* PPS’nin istenen kalıp sıcaklığını (≈150°C) koruyabilmek için kalıbın sıcak su ya da termal yağ kalıp şartlandırıcı cihazları ile ısıtılması gerekmektedir.
* Kalıp plakaları içinde homojen sıcaklık dağılımı sağlanacak şekilde kanal düzeni tasarlanmalı, böylece parça boyunca eşit kristallenme ve düzgün soğuma elde edilmelidir. Yüksek kalıp sıcaklığından dolayı, soğutma suyu yerine basınçlı su (kaynama noktasını artıran basınçlı sistem) veya ısı transfer yağı sirküle eden kalıp şartlandırma cihazları tercih edilir. Kalıbın açılır yüzeylerindeki izolasyon plakaları da ısı kaybını azaltmak için kullanılabilir. Ayrıca kalıp tasarımında, parça geometrisine uygun yolluk ve geçiş kesitleri belirlenmelidir. PPS, akışkanlığı iyi bir malzeme olsa da dolgu oranına bağlı olarak biraz daha yüksek kesitli yolluklar tercih edilebilir.
* Ani kesit daralmaları ve keskin köşeler, dolgu kırılmasına veya malzeme birikimine yol açabileceğinden, kalıp içinde akış kanalları mümkün mertebe düzgün ve akıcı geçişlere sahip olmalıdır.
Robotik ve Otomasyon: PPS’in enjeksiyonla üretildiği hatlarda, robotlar ve otomasyon sistemleri verimlilik ve güvenlik açısından büyük fayda sağlar. Kalıp sıcaklığının yüksek olması nedeniyle parçalar ejeksiyon anında oldukça sıcak olabilir (örneğin kalıp 150°C iken çıkan parçanın sıcaklığı 100°C’nin üzerinde olabilir); bu sıcaklıkta parçaya elle dokunmak pratik değildir. Bu nedenle üç eksenli robot kolları veya lineer çıkarıcılar kullanılarak parça kalıptan otomatik alınır ve soğutma bandına veya fikstürüne bırakılır. Robotik otomasyon, çevrim süresini kısaltmanın yanı sıra insana bağlı hataları da azaltır ve her parçanın tutarlı kalitede üretilmesine katkıda bulunur.
* Örneğin, entegre bir robot sistemi parça çıkarmayı her seferinde aynı şekilde yaparak hem parçaya zarar gelmesini önler hem de üretim hızını artırır. Otomasyon aynı zamanda yollukların otomatik kesilmesi, parça üzerinde gerekiyorsa çapak alma veya kalite kontrol kameraları ile denetim gibi ek süreçleri de kapsayabilir.
* Özellikle yüksek hassasiyet gerektiren PPS parçalarının üretiminde bu ileri otomasyon sistemleri, tutarlı toleransların yakalanmasına yardımcı olmaktadır.
3. Üretim Öncesi ve Sonrası İşlemler
Hammadde Hazırlama:
* PPS granül hammadde, işleme alınmadan önce uygun şekilde hazırlanmaldır. İlk adım olarak yukarıda belirtildiği gibi kurutma işlemi uygulanır. Malzeme kuruduktan sonra, eğer herhangi bir renk masterbatch’i veya katkı karışımı yapılacaksa, bunlar homojen biçimde mal alma boğazına monte edilen dozajlama cihazları ile yapılabilir. Üretim sırasında, yolluk ve çapaklardan çıkan atık malzeme de (toz ve nem içermediğinden emin olunarak) yeniden hammaddeye karıştırılabilir. Ancak geri dönüş malzemesi oranı belli bir seviyeyi aşmamalıdır. Genel bir kural olarak üretilen parçanın kritik özelliklerini bozmadan %20–30 oranında regrind karışımı yapılabilir.
PPS’in Dolgu Malzemeleri ile İşlenmesi:
* PPS genellikle cam elyaf, karbon elyaf veya mineral dolgularla takviye edilmiş bileşikler halinde enjeksiyonla kalıplanır. Dolgu malzemelerinin varlığı, PPS’in mekanik dayanımını ve termal kararlılığını artırırken, işlenme davranışını da etkiler. Lifsel dolgular (cam, karbon, aramid) eriyik viskozitesini yükselterek malzemenin akış mesafesini bir miktar kısaltır ve aynı zamanda parçanın farklı yönlerde farklı çekme oranlarına (anizotropik büzülme) sahip olmasına neden olur.
* Bu, parçada eğilme veya çarpılma riskini artırabilir; dolayısıyla kalıp tasarımında mümkün olduğunca simetrik ve dengeli dolgu akışı sağlanması ve gerekirse parçanın kritik bölgelerinde nervür/rijitlik elemanlarıyla desteklenmesi önemlidir. Mineral dolgular (ör. talk, cam boncuk, kalsit) ise viskoziteyi artırsa da lifler kadar akışı kısıtlamazlar ve toz formda olduklarından parça üzerinde liflerin yarattığı doğrultusal gerilme etkilerini (anizotropi) oluşturmazlar.
* Bu, mineral dolgulu PPS’in genellikle lif dolguludan daha az eğilme riski taşıdığı anlamına gelir. Dolgu tipine bağlı olarak, işleme sıcaklıkları ve hızları optimize edilmelidir. Yüksek cam elyaf içeriği, malzemenin erime sıcaklığını çok değiştirmese de eriyik sıcaklığının üst aralığında çalışılması liflerin matris içinde iyi ıslanması ve parçaya homojen dağılması için faydalıdır.
* Örneğin, %40 cam elyaflı PPS bir bileşiği, saf PPS’e göre daha yüksek bir eriyik sıcaklığında (yaklaşık 330°C civarı) ve hızlı bir enjeksiyonla kalıplandığında, yüzeyde lif izleri minimuma iner ve liflerin parçaya katkısı daha verimli olur. Dolgulu PPS’te ayrıca büzülme oranları düşer; cam elyaf takviyeli sınıflar, unfilled (dolgusuz) PPS’e kıyasla çok daha az kalıptan sonra çekme yapar ve boyutsal hassasiyet sağlar. Bu düşük büzülme sayesinde hassas toleranslı parçalar üretmek mümkün olur ancak kalıbın boyutsal hesapları yapılırken dolgu oranına bağlı spesifik büzülme değerleri dikkate alınmalıdır (örneğin %40 cam elyaflı PPS genellikle akış yönünde ~%0.1, çapraz yönde ~%0.3 gibi düşük büzülmeler gösterir).
* Sonuç olarak, PPS’in dolgu ile işlenmesinde daha yüksek sıcaklık, daha yüksek enjeksiyon hızı ve gerekirse daha yüksek basınç kullanmak yaygın bir pratiktir; fakat aynı zamanda makine ve kalıp aşınma önlemleri de mutlaka alınmalıdır (önceki bölümde bahsedilen sert ekipmanlar, geniş yolluklar vb.). Dolgulu malzemelerde kalıp sıcaklığını da nispeten yüksek tutmak (≥140°C) parçanın iç gerilimini azaltır ve dolgu dağılımının dengeli olmasına yardımcı olur.
Kalıplama Sonrası Isıl İşlemler (Tavlama):
* PPS ile üretilen parçaların büyük kısmı, eğer doğru kalıp sıcaklığında işlendi ise, kalıptan yeterli kristallenme düzeyi ile çıkar ve sonrasında ek ısıl işleme ihtiyaç duymadan kullanılabilir. Yüksek kalıp sıcaklığında (135°C ve üzeri) kalıplanan parçalar, zaten yarı kristalin yapıda ve boyutsal olarak kararlı olacaktır. Bununla birlikte, bazı durumlarda tavlama (annealing) işlemi uygulanır. Özellikle kalıp sıcaklığının düşük tutulduğu (örneğin hızlı çevrim için 80–100°C’de kalıplanmış) parçalar kısmen amorf halde olabilir. Bu parçalar, servis sırasında yüksek sıcaklığa maruz kalacaklarsa, boyutsal değişim yaşamamaları için kontrollü şekilde kristalize edilmelidir. Tavlama, parçaların fırında belirli bir sıcaklıkta bekletilmesiyle yapılır. PPS için cam geçiş sıcaklığı (~90°C) üzerinde herhangi bir sıcaklıkta zamanla kristallenme devam eder, ancak endüstride yaygın uygulama, daha yüksek sıcaklıklarda daha kısa sürelerle tavlamaktır. Örneğin, tipik enjeksiyon kalıplanmış PPS parçalarının nihai kristalliğe ulaşması için 200–230°C aralığında 1–2 saat tavlama yeterli görülmüştür.
* Daha düşük bir tavlama sıcaklığında (ör. 121°C’de) aynı seviyede kristallenme için 4–6 saat beklemek gerekebilmektedir. Tavlama işlemi, malzemede iç gerilimleri giderirken parça boyutlarında bir miktar değişime yol açabilir; parça bir miktar daha fazla büzülebilir ve yüzey görünümü matlaşabilir veya renk tonunda hafif değişim olabilir. Bu nedenle kritik boyutsal parçalar tavlanacaksa, kalıp tasarımı aşamasında bu olası ekstra büzülme payı dikkate alınmalıdır. Yüksek kristalinliğe sahip (sıcak kalıpta üretilmiş) parçalar, 200°C üzerindeki ortamlarda dahi ek tavlama olmadan boyutsal kararlılık gösterirler. Ancak, PPS parçalarının servis sıcaklığını daha da yukarı çekmek (örn. 260°C üzeri sürekli kullanım) isteniyorsa, daha agresif bir ısıl işlem uygulanabilir. Literatürde, PPS parçalarının 271°C gibi sıcaklıklarda 3-4 saat tavlanmasıyla 260°C üzerindeki sıcaklıklarda bile şekil değiştirmeden kullanılabildiği belirtilmiştir.
* Sonuç olarak, tavlama genellikle gerilim giderme ve kristalizasyon tamamlama amacıyla uygulanan bir opsiyonel işlemdir. Tavlama sonrasında parçalar oda sıcaklığına yavaşça soğutulmalıdır (fırın kapatılarak kendi halinde soğumaya bırakma gibi), aksi halde hızlı soğutma nedeniyle yeni gerilmeler oluşabilir. Kalıplama sonrası diğer işlemler arasında, gerekirse post-machining (delik delme, yüzey düzeltme) gibi mekanik işlemler de sayılabilir, ancak PPS oldukça sert ve aşındırıcı olduğundan bu tip son işlemler takım ömrünü etkileyebilir. Bu yüzden tasarım mümkün olduğunca net şekil vermeye yönelik yapılmalı, sonradan minimal işlemler gerektirmelidir.
4. Enjeksiyon Kalıplamada Karşılaşılan Problemler ve Çözümleri
Yüzey Kalitesi Sorunları:
* PPS malzemesiyle kalıplanan parçalarda yüzey kalitesini etkileyen çeşitli faktörler vardır. En yaygın yüzey kusurları arasında akış izleri, matlık veya lif izlieri (takviyeli tiplerde) ve “splay” adı verilen nem kaynaklı izler bulunur. Akış izleri genellikle düşük enjeksiyon hızından veya yetersiz eriyik sıcaklığından kaynaklanabilir; eriyik kalıp içinde ilerlerken soğuyup donarsa yüzeyde dalgalı izler bırakır. Bunu önlemek için hızlı bir enjeksiyon doldurma aşamasında gereklidir. Yüksek hız, eriyik malzemenin kalıp yüzeyine düzgün bir şekilde yayılmasını sağlayarak parlak ve pürüzsüz bir yüzey verir.
* Öte yandan, çok yüksek enjeksiyon hızı da malzeme yanmasına veya kalıp içinde hava sıkışmasına sebep olabilir, bu dengeye dikkat edilmelidir.
* Lif izleri, cam elyafın parça yüzeyinde görünmesi şeklinde olup, genelde yeterince yüksek eriyik sıcaklığı kullanılmadığında veya kalıp sıcaklığı düşük olduğunda ortaya çıkar. Bu durumda, malzeme akışkanlığını artırmak (sıcaklığı yükseltmek) ve mümkünse enjeksiyon hızını artırıp tutma basıncı uygulayarak yüzeyde liflerin geriye çekilmesini sağlamak çözüm olabilir. Splay (nem çizgileri), malzemenin nem içerdiğini gösteren yüzeyde ince gümüşi çizgiler veya kabarcık izleridir. Bunun çözümü, enjeksiyon öncesi reçineyi uygun şekilde kurutmaktır – zira nemli PPS eriyik hale geldiğinde su buharı yüzeye doğru patlayarak bu izleri oluşturur. Eğer yüzeyde buhar çıkışı nedeniyle pütürlü bir yapı gözlenirse, hammadde kuruluğundan emin olunmalı ve gerekirse kurutma süresi uzatılmalıdır.
* Ayrıca kalıp sıcaklığının çok düşük olması da yüzeyde donukluğa neden olabilir; sıcak kalıp yüzeyleri genellikle PPS parçalarda daha iyi bir yüzey finişi verir. Özetle, PPS ile yüksek yüzey kalitesi elde etmek için: uygun kurutma, yeterli eriyik ve kalıp sıcaklığı, optimize edilmiş enjeksiyon hızı/basıncı ve iyi havalandırma kombinasyonu gereklidir.
Kalıp İçi Yanık İzleri:
* Enjeksiyon sırasında parçada görülen yanık izleri (kömürleşmiş siyah/kahverengi lekeler) genellikle hapsolan hava veya gazların sıkışarak aşırı ısınmasından (dizel efekti) kaynaklanır. Kalıbın yetersiz havalandırıldığı bölgelerde, yüksek hızla gelen PPS eriyiği havayı önüne katarak bir cep halinde sıkıştırabilir ve bu hava aniden yüksek sıcaklığa maruz kalıp yanar, sonuçta parçada yanık izi oluşur. Bu problemin birincil çözümü, kalıp havalandırmasını iyileştirmektir. Kalıbın kritik bölgelerine doğru boyutlarda (mikron mertebesinde) havalandırma kanalları eklenmelidir.
* Mevcut kalıpta revizyon imkanı yoksa, enjeksiyon hızını düşürmek geçici bir çözümdür; daha yavaş dolum, hava sıkışmasını azaltarak yanık izlerini hafifletebilir.
* Ancak hızın düşmesi parça kalitesini (yüzey parlaklığı gibi) olumsuz etkileyebileceğinden, ideal olan havalandırma sorununun kalıp üzerinde çözülmesidir. Yanık izleri sadece havadan değil, aynı zamanda malzemenin kendisinin yanmasından da kaynaklanabilir. PPS genelde termal olarak stabil bir polimerdir, fakat çok uzun süre yüksek sıcaklıkta kovan içinde bekletilirse veya önerilen sıcaklık limitlerinin çok üzerinde işlenirse bozunup yanık benzeri kararmış bölgelere yol açabilir. Bu nedenle erime sıcaklığı önerilen aralıkta tutulmalı (genelde ≤340°C) ve malzeme kovanda gereğinden fazla bekletilmemelidir.
* Özetle, yanık izi sorunlarında havalandırma iyileştirmesi, enjeksiyon profil optimizasyonu (hız/basınç kontrolü) ve malzeme sıcaklık süresinin kontrolü ile çözüm sağlanır. Ayrıca sıkışan gazın kalıp içinden atılması için vakum destekli kalıplama sistemleri de bazı hassas uygulamalarda kullanılabilir.
Erime Tutarsızlıkları (Erime İstikrarsızlığı):
* PPS enjeksiyonunda karşılaşılan bir diğer problem, bazı çevrimlerde parçanın tam dolmaması (short shot) veya tam tersi flaş yapması gibi doldurma tutarsızlıkları olabilir. Bu durum, eriyik hacminin veya akış özelliklerinin çevrimden çevrime değiştiğini gösterir. Eriyik tutarsızlıklarının yaygın sebepleri arasında malzeme beslemesinde aksaklık, yetersiz plastikleştirme kontrolü veya makine ekipmanında aşınma bulunur. İlk olarak, enjeksiyon vidasının arkasına uygulanan geri basınç değeri önemlidir. Geri basınç, vidanın malzemeyi ileri itilirken karşılaştığı dirençtir ve eriyik homogenizasyonuna yardımcı olur. Eğer geri basınç çok düşükse, vidanın haznede malzemeyi yeterince karıştırmadan ilerlemesine neden olabilir, bu baskılar arasında eriyik yoğunluğunda dalgalanmalara yol açar. Önerilen geri basınç genelde 2–5 MPa civarındadır; eğer ölçülen dozaj tekrarlanabilirliği hala kötü ise 8–10 MPa seviyelerine çıkarılması vida ortasındaki metering kısmının yani sürtünme sonucu erime kararlılığını artırabilir.
* İkincisi, makinenin roket bilezik kısmının (non-return valve) düzgün çalışıyor olmalıdır. Aşınmış veya sızdıran bir roket bilezik, enjeksiyon sırasında eriyikin geri kaçarak vidanın önünde tutarsız bir yastık bırakmasına neden olur ve her çevrimde farklı miktarda malzeme enjeksiyon yapabilirsiniz. Bu yüzden roket bilezik aşınma durumunu kontrol etmek ve gerekirse yenilemek, tutarlı baskı ağırlığı için gereklidir.
* Üçüncü olarak, vida ve kovan aşınması eriyik tutarsızlığının bir başka sebebidir; aşınmış bir vida, malzemeyi yeterince ileri taşıyamaz veya silindirin duvarlarından kaçaklara izin verir. Yüksek dolgu içerikli PPS işleyen makinelerde zamanla vida hatve uçları ve kovan yüzeyleri erozyona uğrayabilir, bu da dozaj hacminde değişkenlik yaratır. Çözüm, periyodik bakım ve aşınan parçaların (vida, meme, roket bilezik) değişimidir. Meme akıntısı (drool) da eriyik tutarsızlığıyla ilişkilidir: PPS eriyiğinin düşük viskoziteye sahip olması nedeniyle, enjeksiyon öncesi bekleme sırasında memeden kendiliğinden damlaması (akması) mümkündür. Bu olduğunda, bir sonraki enjeksiyon için kovanda daha az malzeme kalacağından eksik baskı meydana gelebilir. Bu sorunu engellemek için, malzemenin iyi kurutulması (nem kaynaklı buhar basıncını önler) ve mümkünse pozitif kapamalı meme kullanılması etkilidir. Ayrıca her çevrim sonrası vidanın bir miktar geriye çekilerek memedeki basıncın sıfırlanması (dekompresyon) standart bir uygulamadır ve akıntıyı büyük ölçüde önler.
* Özetle, PPS enjeksiyonunda eriyik tutarsızlıklarını önlemek için süreç parametreleri dikkatlice kontrol edilmelidir: yeterli ve sabit geri basınç, uygun sıcaklık profili (kovanın her bölgesinde malzemenin tamamen ergidiğinden emin olunmalı), düzgün çalışan makine aksamı ve gerekli ise özel meme/otomasyon önlemleri ile her baskının aynı şartlarda gerçekleşmesi sağlanır. Eğer bütün bu önlemlere rağmen tutarsızlık devam ederse, süreç çıktıları (basınç-zaman eğrileri, eriyik sıcaklık ölçümleri) analiz edilerek sorunun kaynağı (örneğin malzeme partisi tutarsızlığı veya hatalı ısıtıcı bandı gibi) araştırılmalıdır.
Kaynakça: Bu yanıt, PPS üreticilerinin işlem kılavuzları ile mühendislik polimerleri üzerine teknik dokümanlarda sunulan güncel bilgiler temel alınarak hazırlanmıştır. Özellikle Solvay (Ryton® PPS) işlem kılavuzu, Polyplastics (Durafide® PPS) kalıplama önerileri, Celanese (Fortron® PPS) tasarım notları ve MOCOM (Tedur® PPS) işlem önerileri gibi güvenilir kaynaklardaki veriler referans alınmıştır. Ayrıca, enjeksiyon kalıplama konusunda genel mühendislik prensipleri ve sektördeki uygulamalardan yararlanılmıştır. Bu bilgiler ışığında, PPS malzemesinin enjeksiyonla kalıplanmasında optimal koşullar ve ekipman seçimi hakkında kapsamlı bir bakış sunulmuştur.
- 02-04-2025
- 25 dakika
- 2333 kere okundu
- #elektrikli dozaj pompası
- #volumetrik dozajlama
- #SCM-EB
- #sıvı transferi
- #kimyasal dozaj
- #endüstriyel pompa
- #otomatik dozajlama
- #pps
Diğer Haberler
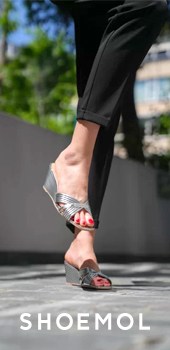